Assistance in a rescue operation
Raising the Kursk
Project details:
Development of a control and software concept for a wave compensation system. / Creation of a simulation model of the lifting process.
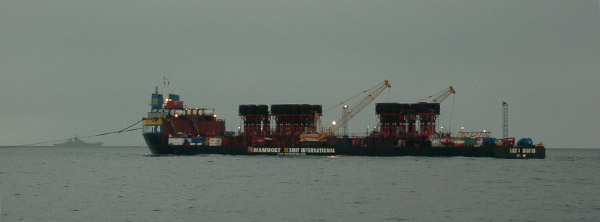
On 12 August 2000, after several explosions on board, the Russian nuclear-powered submarine Kursk sank to the bottom of the Barents Sea, northeast of Scandinavia, to a depth of 108 meters. Of the 118 people on board, there were no survivors.
This brought Russian President Putin his first PR disaster. In order to save his reputation, he therefore promised to rescue the deceased before the end of the following year.
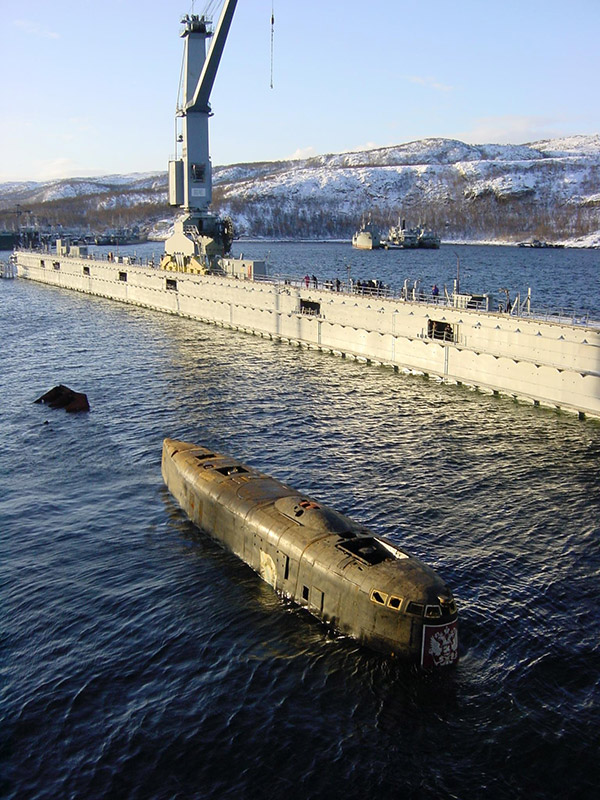
Since the ship was severely damaged by the explosions and two nuclear reactors had to be brought ashore together with the deceased, it was a tight schedule. Nevertheless, it was absolutely necessary to comply with the central requirement of retrieval in 2001.
In June, the Dutch retrieval company Mammoet then initially commissioned IgH with the mathematical modeling of the wave compensators, which consisted of 104 huge pneumatic cylinders, each with 32 connected gas cylinders.
The plant had a total volume of almost 200,000 liters and was operated with nitrogen at pressures between 100 and 160 bar. Its purpose was to ensure that the lifting cables were tightened as evenly as possible, even when the waves were swelling.
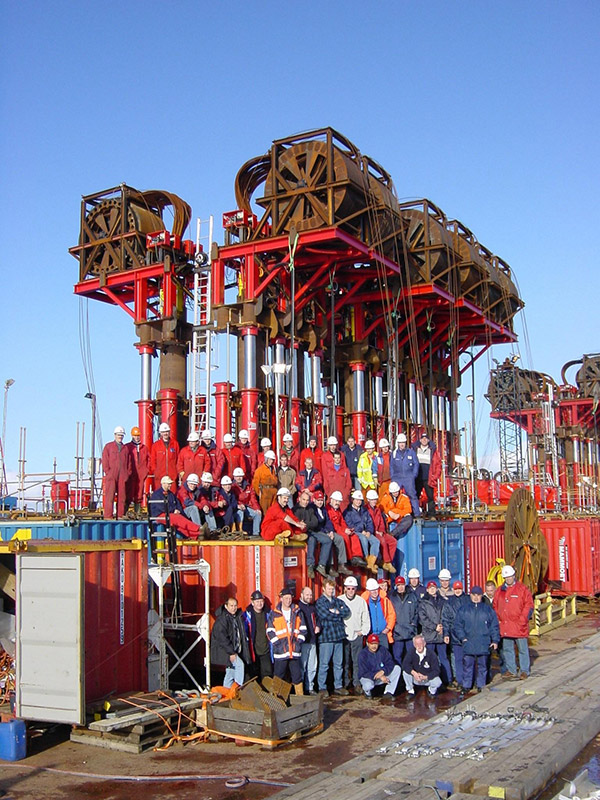
For the retrieval, IgH developed the complete control and software concept for the wave compensation system and implemented it with specialists from the Dutch company Raster. IgH also created a complete simulation model of the entire lifting process to train the operators which operated the five control computers in the control center.
Components of the simulation model:
- the equations of motion of salvage pontoon and Kursk in all six degrees of freedom considering the hydro dynamic forces of the wave motion
- thermodynamical model
- mechanical model of the compensators and lifting mechanism (created with the support of Prof. Dr. Sharma and his assistant Rupert Henn from the Institute of the University of Duisburg)
- complete model of the PLC including the connected sensors and actuators
- interface for control computers
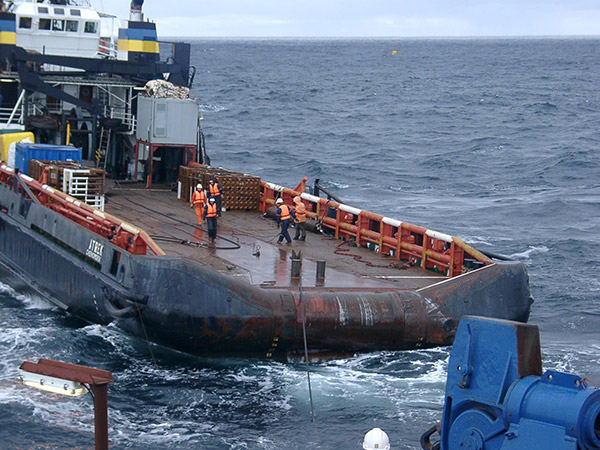
Retrieval process
Via an interface it was possible to operate the control computers either on the PLC in the field or on the simulator. In addition to the training, the optimal reactions to dangerous and unexpected situations could be determined in advance and various retrieval scenarios could be simulated.
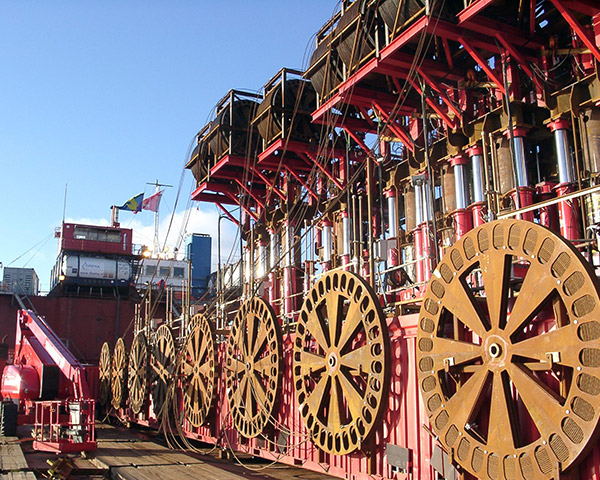
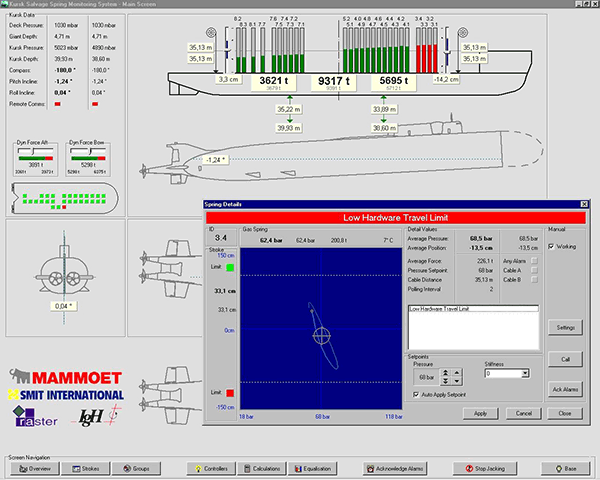
Automatic calculations in IgHs control software enabled the optimal load distribution in the 26 hawser strings where the Kursk was raised. Another special software future was a specially developed control algorithm which adjusted the gas energy in the individual wave compensators corresponding to the optimum load. This procedure was the prerequisite for the safe control of the recovery process at wave heights of up to 3 meters.
Among others, Dr. Rotthäuser and Dr. Hagemeister were responsible for the management of the nitrogen containers.
Your contact persons:
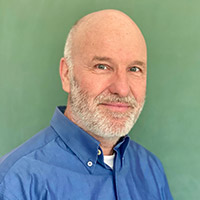
Dr.-Ing. Siegfried Rotthäuser | |
---|---|
Phone: | +49 (0)2 01 – 3 60 14-0 |
E-Mail: |
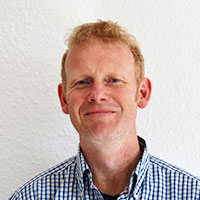
Dr.-Ing. Wilhelm Hagemeister | |
---|---|
Phone: | +49 (0)2 01 – 3 60 14-0 |
E-Mail: |